Overview
Saudi Arabia has never been busier in the warehouse and logistics real estate market. Knight Frank says that key logistics locations in the country are nearly full. The occupancy rate of warehouses in Riyadh is 98%, and Jeddah and the Dammam Metropolitan Area are 97% and 97%, respectively. As vacancy has plunged to near zero, rents are surging and businesses are reconsidering where they can put more storage. The industrial property market that was once stable is now a field of scarcity and innovation.
This boom is being fueled by three key trends: a sudden rise in e-commerce, the investments in the infrastructure linked to the Vision 2030 of Saudi Arabia, and the massive construction and event-driven logistics associated with giga-projects. As landlords and experts in high-spec warehousing are enjoying the benefit, the tight market is posing serious problems. New spaces should not only be able to meet the demand but should be more than expected in terms of design, sustainability, and technology. Such changes demand more than the usual speculation; they need a clever, tactical reboot.
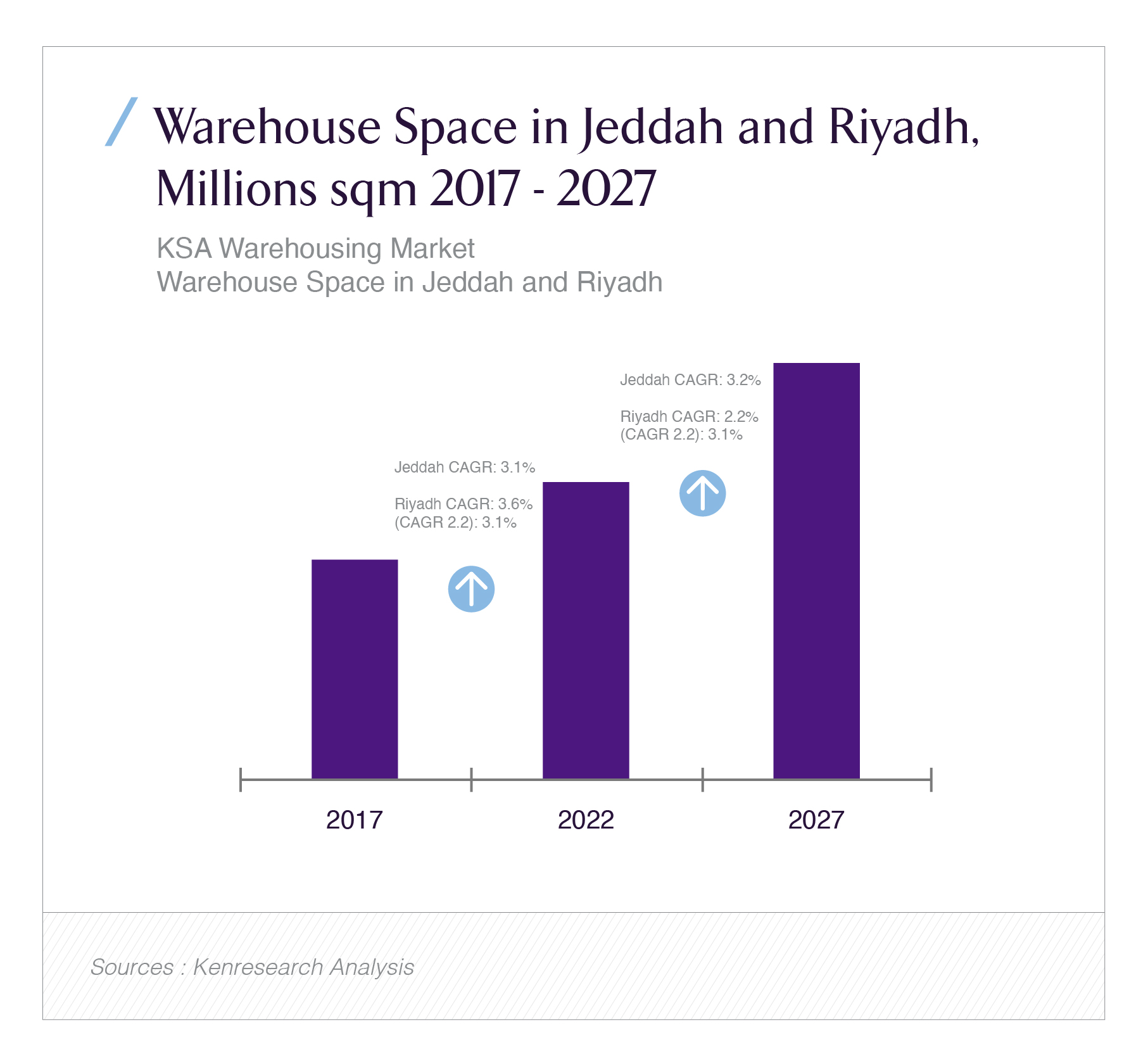
Increasing Occupancy
In the middle of 2024, the report by Knight Frank hit the headlines: Saudi warehouses were practically full. The occupancy rate in Riyadh was impressive at 98%, whereas Jeddah and Dammam were at 97% occupancy. The same report shows that national warehouse occupancy was 97 % at the close of the first half of 2024 across the country. These figures are shocking considering that the optimal vacancy rates are usually between 5-10%, leaving space for turnover and new business.
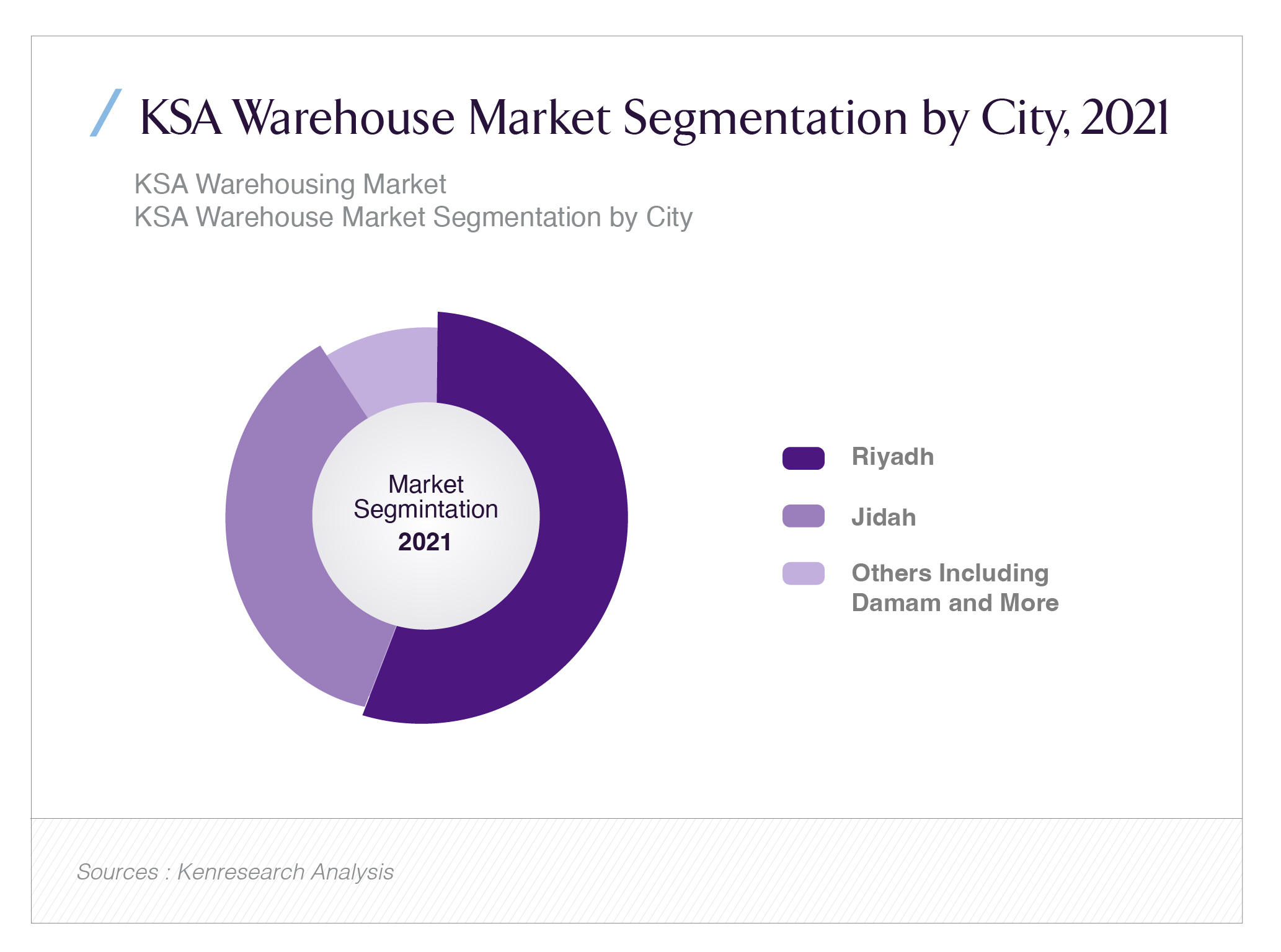
The logistical and industrial inventory of Riyadh alone comprises approximately 28 million square meters but only 820,000 square meters were under development at the end of H1 2024. This trickle of new space has not helped much to relieve pressure. Grade A warehouses, with climate control, high ceilings and automatic loading systems, are virtually unavailable. Although new logistics facilities are still under construction, the shortage is so acute that numerous companies are moving to build-to-suit projects or are ready to pay significantly higher prices.
Growing Rent
The shortage is reflected in the financial part of the rent changes. In Riyadh, rents have increased by 20 % in the first half of 2023 and currently are approximately SAR 190 per square meter, with the most attractive logistics parks being rented at SAR 280 per square meter. Rents increased by 15-22 % to an average of SAR 205 per square meter in Jeddah and 14-15 % to SAR 230-252 per square meter in Dammam.
These are not little price fluctuations; these are large leaps. In most cases, demand leads supply by predetermined margins and this gives the landlords a leeway to increase the prices in case they increase the space. Older warehouses are also renting at higher prices now. Some of the features that tenants are paying for include solar-integrated rooftops, insulated walls, state-of-the-art HVAC systems, and solar readiness. Build-to-suit also allows companies to secure long-term leases and obtain personalized facilities at an even greater price.
Demand Drivers
Many strong forces are driving long-term demand. The first one is the e-commerce boom. Saudi e-commerce has soared, particularly among the younger generations such as Gen Z. This is due to improved internet coverage, new consumer behavior, and the adoption of home delivery during the pandemic. E-commerce already constituted around 8 % of total retail by 2022, and it is projected to be close to 23 % in 2030. It is estimated that fulfillment orders will increase by 13-15 % per annum until 2030. This type of growth requires additional storage near the users and occupiers are booking space near the population centers.
Then there is Vision 2030 and the National Industrial Development and Logistics Program (NIDLP), which are meant to stir things up and diversify the economy. It is envisaged that the contribution of logistics to GDP will increase to 10 % by 2030 and 59 logistics centers with a total area of 100 million square meters will be launched. That count comprises mega-zones such as the Special Integrated Logistics Zone (SILZ), the Sino-Saudi Logistics Zone, and a slew of smaller projects that are emerging around airports and ports. In sum, they are transforming Saudi Arabia into a trading, production, and warehousing center that is open to international giants such as SHEIN and Apple.
Then there are the giga-projects NEOM, Qiddiya, Expo Riyadh, and so on. Such mega-scale projects require the continuous support of staging areas of construction, temporary storage of heavy equipment, and just-in-time supply areas. All that has consumed available warehouse space, adding additional pressure to an already tight market.
Supply Solutions
The old-fashioned speculation of putting up generic warehouses and hoping that tenants will come along will no longer work. The current market demands customized, quality solutions that encompass complicated logistics requirements. Build-to-suit is the order of the day. E-commerce and fast-moving consumer goods (FMCG) firms are ordering custom-made buildings that suit their stock, automation, refrigeration, and floor-space needs. These developments take more time to come into existence and usually cost SAR 300 per square meter or more in design and delivery, but they secure long-term leases and increase operational efficiency.
The lack of land is also driving logistics to vertical warehousing. Although uncommon in non-urban centres, certain parks are experimenting with multi-story storage facilities that have elevators, conveyors and robotics built in. The models have a more expensive initial cost but may provide twice or even three times the space per plot, which is a good trade-off just beyond city limits.
The other priority is sustainability. Most landlords are putting solar canopies on the roofs of warehouses, installing LED lighting, high-quality insulation, and smart energy management systems. Due to the fact that the Kingdom is driving net-zero ambitions and associated ESG criteria, green buildings are favored by international tenants and receive higher rates.
The public-private partnerships are becoming stronger. MODON, the Saudi Authority for Industrial Cities and Technology Zones, is at the forefront in establishing structures that connect industrial zones with parks, ports, and rail lines, particularly the Saudi Landbridge. Such initiatives provide developers with logistical assistance and a realistic plan for gradual warehouse delivery.
Risk Navigation
The market is risky despite the temptation of high rents. The oversupply is a reality- there are too many build-to-suit or vertical projects that may increase the vacancy rates and lead to rent corrections. The developers need to coordinate the deliveries with the tenant pipelines and do it in stages to prevent the flooding of the market.
Another problem is construction costs. Special warehouses are much more expensive to construct as compared to generic ones. Projects with narrower margins can be hurt when the growth of rents slows or halts. Returns are further eaten into by material and labor inflation, which is caused by the huge construction activity associated with giga-projects.
It is also important where it is located. The high-quality land corridors around highways, ports and airports are almost developed. Developers who go further afield need to hedge against delivery risk by investing in rail connections and road improvements- another capital interface. This is to be resolved by projects such as the Saudi Landbridge and logistics zones, but these are time-consuming.
There is also a lack of skilled operations. High-tech warehouses need trained personnel to run them. Sustainability reporting, solar maintenance, advanced inventory systems, and robotics all require expertise. Saudization requirements are aimed at making companies hire local labor, which makes tenants invest in upskilling programs in addition to their storage contracts.
Conclusion
The warehouse market in Saudi Arabia is on the verge of change. Rents are increasing at a rapid rate: 20% in Riyadh, 15-22% in Jeddah and 14-15% in Dammam. This crunch is due to robust e-commerce, national logistics objectives, and new infrastructure that is fed into giga-projects.
Simple solutions are no longer an option for developers, investors, and logistics companies. They require profound, tactical, and multi-dimensional solutions- collaborate with tenants at the initial stage, invest in bespoke designs and green elements, strengthen supply chains with effective planning and infrastructure, and educate local labor. The innovators will win; the ones who remain in old models will lose.
Saudi Arabia provides an example to others: in the digital economy, logistics real estate is not just a property, but infrastructure. Warehouses should be intelligent, agile, and sustainable to support e-business, manufacturing, as well as international commerce. Saudi Arabia is rewriting the rules. In order to compete in the global logistics market, it is necessary to create logistics ecosystems, not simple warehouses.